Slurry Pump Impeller and Slurry Pump Bearing
A slurry pump is a powerful tool for transporting abrasive solids, such as cement, and is typically designed for heavy-duty use. Unlike water pumps, however, slurries have high viscosity and typically require higher horsepower and more rigid shafts. Casings for these pumps are typically made of rubber or metal. In addition, the pump is often equipped with a protective gasket to protect the motor from corrosion, as slurries are heavy.
Slurry pumps are equipped with an impeller that transfers centrifugal force to the slurry. Impellers come in a variety of types, including open, semi-open, and recessed designs. The casing, which typically takes the form of a semi-volute, is a key component of a slurry pump. The impeller is connected to the shaft through a shaft bearing assembly. The shaft bearings are made of wear-resistant materials and are usually designed to prevent the shaft from moving or causing vibrations.
The shaft seal form is another integral part of a slurry pump. It plays an important sealing role between the pump body and the shaft, preventing air and large amounts of water from entering the pump. Centrifugal slurry pumps typically use an auxiliary impeller with a packing seal, which is a hydrodynamic seal that prevents liquid from leaking from the impeller’s outlet. Another integral component of an impeller is a cover plate that sets the back blade with packing or water sealing ring.
A horizontal slurry pump operates on land, while a self-priming pump uses gravity force to move slurries. Its discharge port is below water, and is connected to an enclosure. The slurry enters the pump chamber through a feed port and is discharged through a discharge valve. Both pumps are effective and reliable in a variety of applications. So, whether you need a vertical or horizontal slurry pump, choose one with the right features for your specific needs.
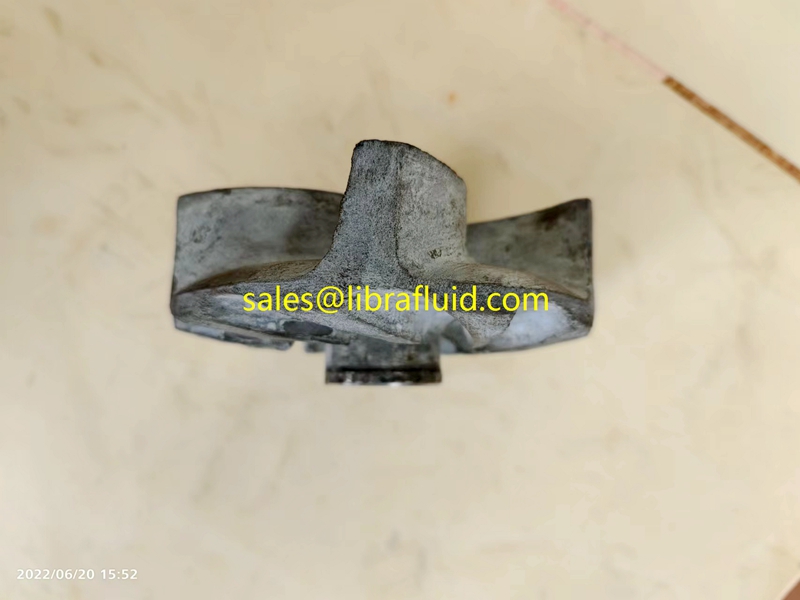
B1127 ceramic slurry pump impeller
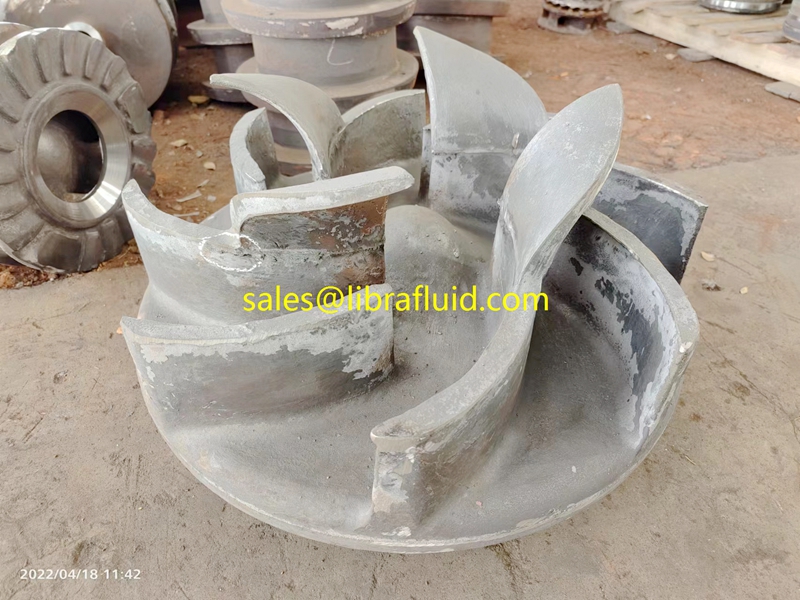
High chrome OEM forth pump impeller