Standard slurry pump operation procedure before running
1. Check if the rotation direction of motor is corresponding to the regulated rotation direction of slurry pump, and please refer to the relevant instruction book. When checking the rotation direction of motor, the motor should be tested alone, and it must not be connected with slurry pump.
2. Make sure that the elastic cushion of coupling is correct and complete.
3. Detect the concentricity of motor shaft and slurry pump shaft.
4. When turning the slurry pump (including motor) manually, user should not feel uncomfortable, such as friction, tight, etc.
5. The bearing oil in the bearing box should reach the level indicated by the oil pointer.
6. Before the slurry pump starts, seal water (cooling water for mechanical seal) needs to be added first. At the same time, the inlet valve is opened and the outlet valve is closed.
7. Make sure that the valves are reliable and in normal state.
8. The pipe system should be reliable, firm, and installed correctly. In addition, other parts also need to be detected, such as anchor bolt, flange sealing gasket and other bolts.
Starting, Running and Monitoring
1. As illustrated above, the inlet valve should be opened and the outlet valve should be closed before the slurry pump is started. Then, the machine is started, and the outlet valve is opened slowly. In addition, the opening speed and degree should be controlled to a certain level during which slurry pump vibration is avoided and the current of motor is not over rated current.
2. For the slurry pumps installed in series, the above procedure is also suitable. When the primary pump is started, the outlet valve of last pump can be opened to some degree, and the motor current of primary slurry pump is 1/4 of rated current when this valve is opened. Then, the secondary pump, the tertiary pump and other pumps are opened one after another until the last pump. After all the pumps are started, the outlet valve of last pump can be opened wider and wider gradually, and the opening speed and degree is controlled to avoid pump vibration and the motor current of every pump should not higher than the rated value.
3. Slurry pump is mainly used for transferring liquids, so, flow meter is recommended for the monitoring system to make sure that the flow rate meets requirement at any time. On the other hand, the outlet of pipe is required to have a certain level of pressure for the slag-washing system, filter pressing dehydration system and pipe system equipped with swirler. Thus, pressure gauge needs to be installed to monitor the pressure.
4. Along with the pressure and flow rate, the current of motor is also detected to make sure that it is not over the rated current. Meanwhile, other items are real-time checked, such as if there are any abnormal phenomena for oil seal, bearing and other parts, if evacuation or spilling takes place in the pump, etc.
Slurry pump operation Daily Maintenance
1. Air leakage should be avoided for the suction pipeline system, and the screen should prevent large particle or long fiber from entering into the slurry pump which may lead to the block of slurry pump.
2. Expendable parts need to be replaced in time. The repair and assembly must be correct, and the gap is reasonably adjusted. Also, friction and tight problem should be avoided.
3. The pressure and quantity of seal water should meet the specifications, and adjust the tightness of packing at any time, or replace the packing in order to prevent the slurry leakage. In addition, the shaft sleeve also needs to be changed in time.
4. When changing the bearing, there should be no dust in bearing assembly. The lubricating oil is clean, and the temperature of bearing had better be lower than 60-65°C when the pump is running, and the maximum temperature is 75°C.
5. The concentricity of motor and pump should be ensured, and the elastic cushion of coupler is complete and properly installed. If the elastic cushion is damaged, please replace it timely.
6. The components and pipe system of slurry pump must be firm, reliable and correctly installed.
Assembly and Disassembly
1. The assembly and disassembly of slurry pumphead, and the gap adjustment should be carried out according to the assembly drawing.
2. Please refer to the assembly drawing to execute the assembly and disassembly of packing seal. In order to guarantee the sealing effect of packing seal, the opening of packing should be cut into a specific shape. When it is added into packing box, openings of adjacent packing should form an angle of 108 degrees.
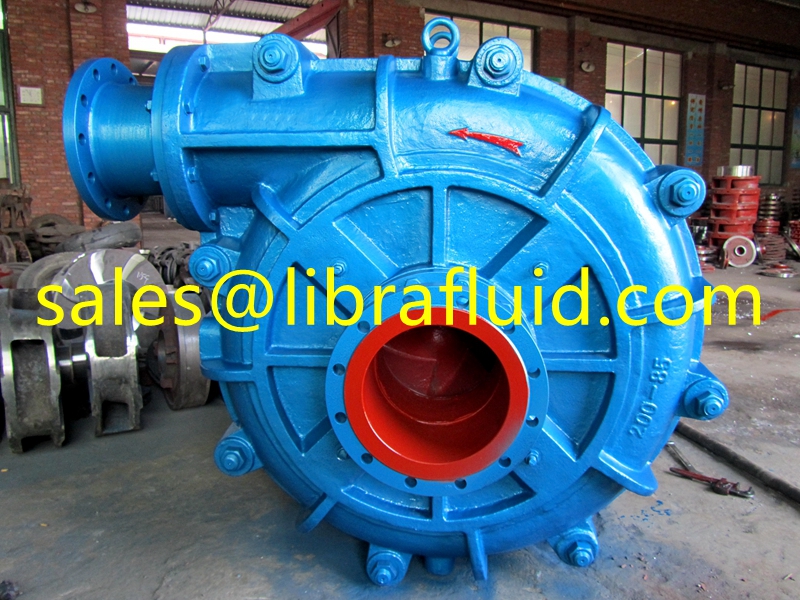
8 inch heavy duty slurry pump